ECOncrete – Reducing the Carbon Footprint of Concrete Based Coastal and Marine Infrastructure
Case study by: Raviv Shirazi, Dr. Ido Sella, Dr. Shimrit Perkol-Finkel
Scientists claim that at least 5% of humanity’s carbon footprint comes from the concrete industry, both from energy use, and from the carbon dioxide by-product associated with the production of cement, one of concrete’s principal components.
Concrete is the main construction material globally, accounting for over 70% of Coastal and Marine Infrastructure (CMI) such as ports, coastal defence structures and waterfronts. Standard Portland cement based concrete CMI support low biological diversity and are typically dominated by nuisance and invasive species.
ECOncrete®’s bio-enhancing concrete products have a reduced carbon footprint compared to Standard Portland cement based concrete, due to a combination of proprietary admix integrating by-products and recycled materials, and unique ability to enhance biological process such as biocalcification and photosynthesis which facilitate CO2 assimilation.
A Concrete Problem
With nearly half of the human population living along coastlines[1], coastal development, and increasing coastal urbanization are inevitable. Concrete is the main construction material globally, accounting for over 70% of Coastal and Marine Infrastructure (CMI)[2]. Nonetheless, it is a poor substrate for biological recruitment, and is considered toxic to many marine organisms, mainly due to its unique surface chemistry which impairs the settlement of various marine larvae[3-6]. Subsequently, concrete based CMI commonly attract low diversity biological communities which are primarily dominated by invasive species and very different to those typical in natural habitats[7, 8]. Concrete’s carbon footprint is fairly large due to two factors[9]:
- The use of fossil fuels in the burning process to heat limestone (CaCO3) in kilns to form CaO, one of the major components in cement.
- The large quantities of carbon dioxide released during Calcination, the conversion of limestone to CaO proceeds.
According to the most recent survey of Portland Cement Association (PCA), an average of 927 kg (2044 lb) of CO2 are emitted for every 1000 kg (2205 lb) of Portland cement produced in the U.S[10].
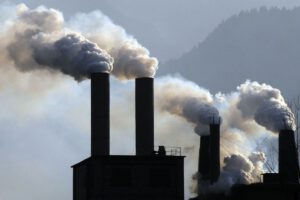
Smoke billows from a cement plant
Low Carbon Solution
ECOncrete offers science based solutions that reduce the ecological footprint of CMI, through a suite of high performance environmentally sensitive concrete technologies that enhance the biological and ecological value of CMI while increasing their strength and durability. An innovative combination of bio-enhancing concrete admixtures, increased micro and macro surface roughness, and unique 3D designs, enhance the growth of diverse marine plants and animals on ECOncrete products. These organisms provide a wide array of biological and ecological advantages, including high biodiversity, enhanced ecosystem services, improved aesthetics, and Bioprotection due to the biological communities encrusting the concrete[11, 12]. A significant environmental advantage of ECOncrete technologies is a substantial reduction of carbon footprint in all of the company’s products. This is due to two main pathways: 1) the unique properties of ECOncrete’s admix, which integrates by-products and recycled materials, 2) biological processes including calcification by organisms such as oysters, corals and tube worms and the primary production by photosynthetic organisms through marine flora.
Reduced Carbon Footprint through ECOncrete Admix
While the terms cement and concrete are often used interchangeably, cement is an ingredient of concrete that, when mixed with water, sand and gravel, forms concrete. Concrete has a high carbon footprint mostly due to high content of Portland cement in the concrete. Between 50- 60% of the CO2 emitted during the production of cement results from calcination of calcium carbonate raw materials, the remaining CO2 emitted results from burning fossil fuels[13]. ECOncrete addresses the global need for reducing the carbon footprint of CMI by significantly reducing the amount of Portland cement in the mix compared to standard marine grade concretes. This is achieved by replacing portions of the cement with supplementary cementitious materials (SCMs). The use of SCMs in concrete work in combination with Portland cement is performed to improve strength and durability, in addition to reducing the CO2 embodied in concrete by as much as 70%, with typical values ranging between 15 – 40%[13]. The SCMs utilized in ECOncrete products are various calcium carbonate based pozzolans, mostly, industrial byproducts which would otherwise end up in landfills. Moreover, all of ECOncrete’s products are manufactured using slag cement (containing ground granulated blast-furnace slag – GGBS) further reducing the products’ CO2 footprint. Slag cement is commonly used as a partial substitute for Portland cement in concrete at a replacement level of up to 50%. When slag cement replaces 50% of the Portland cement, greenhouse gas emissions per cubic yard of concrete are reduced by 45%[14]. For example, while an average of 931 kg of CO2 are emitted for every 1000 kg of ordinary Portland cement, GGB emits only 26.5 kg[15]. As ECOncrete admix uses innovative combinations of slag cement with SCM, we are able to produce concrete products that have as much as 80% less carbon footprint compared to standard Portland cement based concrete products.
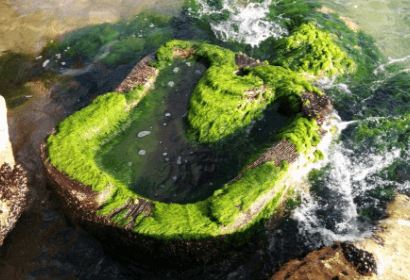
ECOncrete Tide Pool blooming with green algae
Carbon Footprint Reduction through Biological Processes
The oceans are a significant sink for atmospheric CO2, removing approximately 30% of current anthropogenic CO2 emissions[16]. In addition, certain biological processes facilitate carbon assimilation and uptake.
Carbon is assimilated into skeletons of marine organisms like oysters, corals, tube worms, coralline algae, and barnacles, in a process called biocalcification[17]. As an integral part of the organism’s growth, it produces a calcitic skeleton. As evident from the chemical equation of the process:
- CO2(g) ↔ CO2(aq)
- CO2(aq)+H2O↔H2CO3
- H2CO3↔HCO3–+H+
- 2HCO3–+Ca2+↔CaCO3+H2O+CO2
two CO2 molecules are used for generating CaCO3, of which, one is assimilated into the CaCO3 and the other is released as CO2. The bottom line is that for each unit of CaCO3 produced, Dissolve Inorganic Carbon (DIC) is reduced by one unit and alkalinity by two units.
While clearly for every mole CaCO3 formed, one mole of CO2 is produced, yet another CO2 is embedded into the CaCO3 formed. Frankignoulle, Pichon[18] notes that due to the buffering capacity of the seawater, the ratio between CO2 released and CaCO3 participated is about 0.6. Nonetheless, the released CO2 is mainly converted to HCO3[19], and In the short term (hours to days), some or all of the CO2 liberated during carbonate deposition may be absorbed by biological processes on the reef[20].
The potential carbon storage in calcitic skeletons of marine organisms is vast. One Calcium carbonate molecule (composed of 1 Calcium atom [40.078 g/mole], 1 Carbon atom [12.011 g/mole] and 3 Oxygen atoms 47.997 [g/mole]) have a molecular weight of 100.086 g/mole. Thus, in every 1000 g of CaCO3, 120 g of Carbon are stored.
For example, in crushed whelk shells CaCO3 accounts for 95% of the shell material[21]. With one gram of CaCO3 containing 0.119 g carbon (by division of molecular weights), it was estimated that for each tone of shell material there is 0.091 tone of avoided CO2 emissions[22]. Similarly, Ware, Smith[20] assessed a reasonable regional average for gross CaCO3 production of reef provinces (as defined in Smith[23]) is approximately 1.5 [±0.5 ]kg CaCO3 m-2y-1 corresponds to 180 [ ± 60]g C m-2y-1.
Sella and Perkol-Finkel[24] demonstrate that ECOncrete units enhance growth of engineering species such as oysters, serpulid worms, bryozoans and coralline algae significantly more than control Portland cement units. These engineering species (oysters, serpulid worms, barnacles and corals) deposit CaCO3 skeletons onto hard surfaces thus creating valuable habitat to various organisms[25] while also contributing to the structures’ strength, stability and durability[11].
According to Perkol-Finkel and Sella[3] biocalcification onto ECOncrete’s M4 bio-enhanced units averaged at 659.51 g m-2y-1 in temperate Mediterranean Sea environment, and 249.72 g m-2y-1 in a tropical Red Sea environments, with maximal values reaching 1000 g m-2y-1. This rate corresponds to maximal storage of 120 g of Carbon for every square meter of ECOncrete infrastructure yearly.
Notably, in the same study, values of biocalcification on control Portland cement based concrete units were significantly lower, averaging 334.48 g m-2y-1 in temperate, and 168.68 g m-2y–1 in a tropical environments.
Obviously the amount of CaCO3 produced varies from one ecosystem to another, and depending on community structure. For example, Hily, Grall[17] calculated the CaCO3 production of various calcified species along the rocky shores of Brittany, France, and found that in sheltered sites Oyster CaCO3 production rates were 2390 g CaCO3 m-2 y-1. Values for coralline algae vary from 10 to 10,000g CaCO3 m-2y-1 in tropical areas[26], and remain lower in temperate waters (876g CaCO3 m-2 y-1)[27].
Photosynthesis performed in the marine environment mostly through macro and micro-algae, seagrasses and via symbiotic algae such as the ones residing in coral tissue, acts as a CO2 sink, through the formation of organic matter:
(1) 6H2O + 6CO2→ C6H12O6 + 6O2
Photosynthesis also removes CO2 from shallow ocean waters, and downward flux of the organic compounds generated through the process can effectively store CO2 in the deep ocean for hundreds of years[28].
According to Perkol-Finkel and Sella[3] ECOncrete’s bio-enhanced units had a significantly higher Chlorophyll a content compared control Portland cement based concrete units, which is indicative to enhanced primary production through photosynthesis. This was true for both temperate and tropical environments. Thus, ECOncrete has the potential to enhance photosynthesis compared to “gray” concrete, thus further reducing the structures’ carbon footprint by harnessing natural processes.
References
- Sharma, P., Coastal Zone Management. 2009: Global India Publications. 307 pp (Accessed March 2015) ISBN 978-81-907941-0-7. 307 pp (Accessed March 2015) ISBN 978-81-907941-0-7.
- Kampa E and Laaser C, Heavily Modified Water Bodies: “Information Exchange on Designation, Assessment of Ecological Potential, Objective Setting and Measures” – Updated Discussion Paper, in Common Implementation Strategy Workshop Brussels, 39 pp. 2009.
- Perkol-Finkel, S. and I. Sella. Ecologically Active Concrete for Coastal and Marine Infrastructure: Innovative Matrices and Designs. in From Sea to Shore–Meeting the Challenges of the Sea. 2014. Edinburgh, UK: ICE Publishing.
- Lukens, R.R. and C. Selberg., Guidelines for Marine Artificial Reef Materials, in A Joint Publication of the Gulf and Atlantic States Marine Fisheries Commissions. 2004.
- EBM, ENVIRONMENTAL BEST MANAGEMENT PRACTICE GUIDELINE FOR CONCRETING CONTRACTORS. 2004.
- McManus, R.S., et al., Partial replacement of cement for waste aggregates in concrete coastal and marine infrastructure: A foundation for ecological enhancement? Ecological Engineering, 2017.
- Dafforn, K.A., et al., Application of management tools to integrate ecological principles with the design of marine infrastructure. Journal of environmental management, 2015. 158: p. 61-73.
- Firth, L.B., et al., Between a rock and a hard place: Environmental and engineering considerations when designing coastal defence structures. Coastal Engineering, 2014. 87(0): p. 122-135.
- NSF, National Science Foundation. “How Solid Is Concrete’s Carbon Footprint?.” ScienceDaily. ScienceDaily, 24 May 2009. <www.sciencedaily.com/releases/2009/05/090518121000.htm>. 2009.
- Marceau, M., M.A. Nisbet, and M.G. Van Geem, Life cycle inventory of portland cement manufacture. 2006, Portland Cement Association IL.
- Risinger, J.D., Biologically dominated engineered coastal breakwaters. 2012, California State University.
- Naylor, L.A., et al., Facilitating ecological enhancement of coastal infrastructure: The role of policy, people and planning. Environmental Science & Policy, 2012. 22: p. 36-46.
- NRMCA, Concrete CO2 Fact Sheet February 2012 2012.
- PCA. Portland Cement Association Green in Practice 107 – Supplementary Cementitious Materials (SCMs) https://www.concretethinker.com/technicalbrief/Supplementary-Cementitious-Materials.aspx.
- Yang, K.-H., et al., Effect of supplementary cementitious materials on reduction of CO 2 emissions from concrete. Journal of Cleaner Production, 2015. 103: p. 774-783.
- Siegenthaler, U. and J. Sarmiento, Atmospheric carbon dioxide and the ocean. Nature, 1993. 365(6442): p. 119-125.
- Hily, C., et al., CO2 generation by calcified invertebrates along rocky shores of Brittany, France. Marine and Freshwater Research, 2013. 64(2): p. 91-101.
- Frankignoulle, M., M. Pichon, and J.-P. Gattuso, Aquatic calcification as a source of carbon dioxide, in Carbon sequestration in the biosphere. 1995, Springer. p. 265-271.
- Zeebe, R.E. and D.A. Wolf-Gladrow, CO2 in seawater: equilibrium, kinetics, isotopes. 2001: Gulf Professional Publishing.
- Ware, J.R., S.V. Smith, and M.L. Reaka-Kudla, Coral reefs: sources or sinks of atmospheric CO 2? Coral reefs, 1992. 11(3): p. 127-130.
- White, M.M., et al., The concentration of calcium carbonate in shells of freshwater snails. American Malacological Bulletin, 2007. 22(1): p. 139-142.
- Dennis, H.D., et al., Reefcrete: Reducing the environmental footprint of concretes for eco-engineering marine structures. Ecological Engineering, 2017.
- Smith, S., Coral-reef area and the contributions of reefs to processes and resources of the world’s oceans. Nature, 1978. 273(5659): p. 225-226.
- Sella, I. and S. Perkol-Finkel, Blue is the new green–Ecological enhancement of concrete based coastal and marine infrastructure. Ecological Engineering, 2015. 84: p. 260-272.
- Jones, C.G., J.H. Lawton, and M. Shachak, Organisms as ecosystem engineers. Oikos, 1994. 69(3): p. 373-386.
- Payri, C.E., Production primaire et calcification des algues benthiques en milieu corallien. Oceanis, 2000. 26(3): p. 427-464.
- Potin, P., et al. Annual growth rate of the calcareous red alga Lithothamnion corallioides (Corallinales, Rhodophyta) in the Bay of Brest, France. in Thirteenth International Seaweed Symposium. 1990. Springer.
- Kleypas, J.A. and C. Langdon, Coral reefs and changing seawater carbonate chemistry. Coral reefs and climate change: science and management, 2006: p. 73-110.